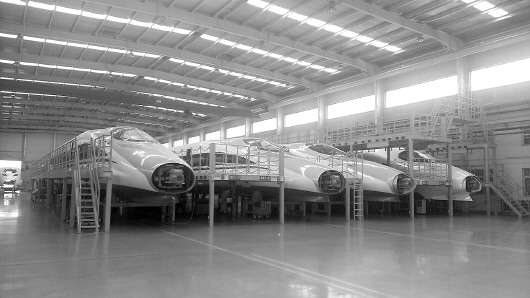
南车四方的“巨无霸”车间,等待总装的高铁列车。 本报记者 马绍栋 摄
本报记者 马绍栋 姜宁
在“7·23”动车追尾事故之前,中国高铁一直演绎着日德等国家都无法想象的神话,尤其是列车时速。
京沪高铁这个“新手”试运行时,6分钟内时速飙至302公里,这让日本人为之惊叹,“日本从200公里跑到300公里用了50年,这里只需要5年。”
在高速发展的中国,“效率”成为高铁最有力的注脚。“7·23”事故之后,中国高铁开始谨慎对待“效率”这个词。如何迈过3年前的这道门槛儿?在中国企业冲刺高端制造业的过程中,消除浮躁,秉持真正的专业精神,这是必须学会的一课,也是中国制造从骨子里必须注入的灵魂。
降速里的信号
“时速350公里的高铁是什么感觉?想想,如果将车体虚化,在空中距离1.5米的高度,以每秒钟100米的速度飘行……”
这是2010年12月,CRH380A试运行时,时任铁道部副总工程师兼运输局局长张曙光向记者描述坐高铁能享受到的“神仙”般感觉。
当年10月,南车研制的CRH380A动车在京沪高铁实验中创下了486.1公里的世界高铁运营试验的极速体验。
当时,时任铁道部部长刘志军在驾驶室亲自督阵,要求驾驶员冲到极限速度并长期保持。陪同的外方工程师心惊肉跳,高呼减速,而刘志军面不改色。
“开,老子一个部长都不怕,你怕什么。”这是网传刘志军在现场说的话。
在高速发展的中国,“效率”成为高铁最有力的注脚。
“7·23高铁事故后,我们把运行速度降慢了一些,目前最高时速486.1公里的高铁列车,从原先的300公里以上的时速,降低到了200多公里的时速。”南车四方副总工程师邓小军对本报记者说,走还没有完全学会,跑起来一定摔跤。7·23这起事故让他深切体会到,中国高铁在快速追赶的步伐中,追求安全比追求速度更重要,这是不可逾越的底线,无论什么原因和理由。
一直在超车道上行驶的中国高铁开始减速。事关国家面子,上上下下非常敏感。“这是安全性在中国受到重视的最重要的信号。”就在国内媒体对高铁降速一片质疑时,国外舆论对此却是反应积极,英国《金融时报》东京分社社长王明撰文指出,“这传递出一种以更慎重态度对待高铁的信号。糅合各家技术、试验信号和管理系统,以及建设高质量基础设施,是需要时间的。在国内取得良好的记录,是将来在海外获得成功的最佳基础。中国高速列车行业应避免欲速则不达。”
质量工程师一天跑10公里
事故发生后,南车把出事的车厢拉回来,再解体,对所有部件一一分析。这些损毁的车厢,是最宝贵的“教材”。
“中国的高铁技术不会因为某一次事故停止发展。”郑昌泓对本报记者说,高速铁路发生事故各国都出现过,虽然这次事故和动车质量没有什么关系,但给了南车很多警示,在控制系统和管理方面有很多需要调整的地方。
对列车质量的高度重视,从南车四方的机构设置上可见一斑。
整个南车四方员工总数7700多名,负责研发的技术中心不到500人,而确保每辆列车质量的质量管理部人数超过500人,这个数字几乎赶上一个中型企业的总员工数。
在这个庞大的部门中,像李彦林这样的“质量工程师”占了大多数。“质量工程师必须既懂管理又懂技术,两者缺一不可。”李彦林说,南车四方的新晋员工必须在生产一线工作6-12个月,充分熟悉列车的各个零部件、生产工序、流程后,才有资格加入质量工程师队伍。
这500多人按职责分为几类,80-100人为策划人员,大部分是大学生,负责指挥施工人员怎么干,确定检查内容和频度,就像一个转向架过来,按规定看对角线、平整度、对称度、孔的间距;还有100多人搞无损探伤,这一环节尤其重要,一旦出现漏检后果不堪设想;另外还有200多人的专业质检队伍,检测过程涵盖供货商、生产设备、工艺流程、成品出厂等环节。
在拥有车体、总组装等40余条生产流水线这样的“巨无霸”公司里,可以想象,高铁单节车厢有多长,南车四方的车间就有多大,而李彦林的大量工作是到一线检测,从这个工序到那个工序,发现问题再回来开会解决,一天来来回回得跑10公里。
现在自动化检测设备那么发达,为什么还要人工跑来跑去?事实上并非如此。就一些产品特性来看,许多零部件没有达到自动化管控水平,同时受制于整个工业链上的水平,一部分工程师还要在供货商的生产线上管控,只有管好过程才能管控结果。
每一位质量工程师都要有一双“透视眼”,“就像墙上出现了窟窿,老百姓拿泥一糊就行了,而我们必须分析背后原因,而且一定要从根源上解决,否则将来会出大问题。”李彦林说,比如焊接,光看焊缝没用,必须看生产过程,包括电流电压、气体保护流量、焊丝用得对不对等指标,一旦形成产品了,就分辨不出用什么焊丝了。
从骨子里形成惯性
今年4月,时速250公里动车组第17列调试试验时,质量部人员听到该车一转向架疑似有漏风声,进一步检查发现,转向架空气弹簧支撑梁管座焊缝表面有一个微小气孔,用肥皂水检查发现气孔处轻微漏风。
转向架对动车来说相当于汽车底盘,这种微小气孔造成的影响就是一个螺栓特性指挥不灵。当时总装部急等这个架子用,急得不行,一旦拖延整个生产计划就完不成。领导严肃地问李彦林,修复要多大成本?
“修复问题不大,就是需要时间。”李彦林说。
“返工吧,我们宁可被考核、被批评。”领导说。就这样,尽管当时生产任务异常紧急,但质量部还是决定返工,连夜加班焊修,做保压试验,直到第二天早上10点才交付。
“这样的返工肯定影响生产计划考核,我们没到100%,但转向架交出去后我们心里放心,等出了问题再弥补,后果可想而知。”李彦林说,“全员质量管理”每家企业都在喊,但真正落实到位必须有极大魄力。一旦质量管理和交付计划冲突了、和钱冲突了,一般企业往往就把质量踩在脚底下。而高铁这样的高端制造业,质量问题容不得半点疏忽,绝对是要“一票否决”的。每个造动车的人骨子里要形成一种惯性,习惯于从粗放型生产向精细化生产转变,树立一种专业精神。
今年5月,时速250公里高寒防风沙动车组在整列编组通电后,质量工程师发现客室顶板表面喷漆不均、有色差现象,这种情况不通电难以发现。这类动车组是试制车辆,并非运营商品车辆,而且出厂试验任务急,这种色差缺陷并不影响车辆性能,完全可以忽略。
但最终,为确保整车商品化程度,公司决定将整列顶板更换。这种情况属于重大返工。同时,为避免类似事情发生,在车辆编组前单车细检工序中,又增加了车辆通电照明这一程序,以防止色差。
必须严防死守
高速列车整车包括4万多个零部件,涉及机械、冶金、电子、化工等多个行业,整个产业链涉及多达500余家。如此庞大的供应商队伍若有一家搞点小动作,整个列车的运行安全便遭遇重大挑战,对供应商的质量管理是一个绕不开的课题。
要成为南车四方的供应商有多难?南车设置的一个多达1000分的质量评价手册,这是供应商必须迈过的门槛。
这1000分仅仅是对供货商的前期评价,涵盖了人员能力、产地、财务状况、供应商管理水平、产品制造过程、工艺水平、实物质量等九大方面,要命的是其中包含很多否决项,就是说其他方面得分再高,可能一个指标不合格就全部作废。
“比如A类零部件,即影响车辆整体安全的关键部件,打分要求低于80分免谈,这仅仅是第一关。”李彦林说,第一次供货,技术专家、质量工程师要对整个产品过程进行认可。进一个产品要做3次评估,如果不稳定还有专项检查;你原先不供这个产品,现在供了,程序必须全部走一遍;如果原先供螺钉的,现在供螺母,对不起,还要从头重新做一遍。“我们不怕折腾,就是要告诉对方,要想给南车供货,就老老实实干好,别心存侥幸。”
每次评估供货商,南车四方要去4-6人,持续两到三天。沈阳一家意向企业,光综合评估就做了3次,另外一项评估2次,监督审核2次。南车四方累计去过15个工作人员,检测项目300多项,多的时候要提50-60项问题,当场出初步结果。
“没有人愿把伤疤露给你,必须严防死守。”李彦林说,现在南车四方正策划把供应商的数据进行信息化管控,几十个质量工程师在产品进厂前对现场评估,实验过程等管控,“就像买水果,摆出来的都是好苹果,我们会看摊主买的什么肥料、用的种子、是否按规则浇水,结果是放心的,那么最后果园里的苹果是可以买的。”
本稿件所含文字、图片和音视频资料,版权均属齐鲁晚报所有,任何媒体、网站或个人未经授权不得转载,违者将依法追究责任。